圓柱正弦活齒減速器的加工及試驗研究
6.1圓柱正弦活齒減速器樣機的加工制造
圓柱正弦活齒減速器是為適應(yīng)航空航天、石油開采等特種工作環(huán)境的需要,而自行開發(fā)研制的一種微小型活齒傳動裝置。本文經(jīng)過空間嚙合理論、強度及動力學(xué)特性分析等一系列理論研究,對圓柱正弦活齒減速器進行了多目標(biāo)動態(tài)優(yōu)化設(shè)計,最終研制出一臺最大外徑為 80mm,傳動比為5,輸出扭矩為20N·m的微小型減速器樣機。
由圓柱正弦活齒減速器的結(jié)構(gòu)組成可知,其中大部分結(jié)構(gòu)都是常用的零件,故可用傳統(tǒng)的加工方法及通用的加工設(shè)備進行加工制造。而殼體及主動軸的內(nèi)、外空間正弦滾道的加工制造是該減速器制造的關(guān)鍵技術(shù)及難點,它們加工精度的高低及質(zhì)量好壞直接影響著該活齒傳動的傳動性能。由于內(nèi)、外正弦滾道為空間齒廓曲面,形狀復(fù)雜,要求加工刀具不但要有x,y,z三個方向的進給運動而且還要求刀具主軸能繞y,z軸轉(zhuǎn)動,因此無法在普通銑床上加工制造,需要依靠五軸數(shù)控(NC)機床來實現(xiàn)并保證滾道加工的精度和質(zhì)量。
數(shù)控(NC)機床是裝有程序控制系統(tǒng)的機床,該系統(tǒng)能夠邏輯地處理具有使用編碼或其他符號指令規(guī)定的程序。而同時具備自動換刀功能及自動判斷被加工件上多個表面功能的NC機床,稱為加工中心。數(shù)控機床具有如下特點:能加工復(fù)雜型面零件;加工精度高,加工過程中,能在一次裝夾定位中加工多個表面,并能完成自動檢測等工序,有效的提高了生產(chǎn)效率;自動化程度高;可以實現(xiàn)一機多用;采用數(shù)控機床,促進了單件、小批量生產(chǎn)自動化的發(fā)展,實現(xiàn)柔性自動化生產(chǎn);只需更換程序,采用通用工夾具,就可適用不同品種及尺寸規(guī)格零件的自動化生產(chǎn);谝陨咸攸c,對于單件、中小批量生產(chǎn),形狀復(fù)雜、精度要求高的零件加工采用數(shù)控機床生產(chǎn),可以提高產(chǎn)品質(zhì)量,降低生產(chǎn)成本,獲得較高的經(jīng)濟效益。
本課題利用瑞士米克朗公司生產(chǎn)的UCP1350五坐標(biāo)數(shù)控加工中心進行空間正弦滾道的加工(如圖6-1),瑞士米克朗公司于1908年成立于瑞士比爾,是世界著名的精密機床制造商,在機加工領(lǐng)域積累了數(shù)十年的經(jīng)驗。多年來,米克朗公司始終保持著在制造五軸聯(lián)動加工中心方面的領(lǐng)先地位,并投入了大量的力量用于發(fā)展銑削技術(shù),不斷推出新型的高速高性能加工中心。其中五軸聯(lián)動加工中心為復(fù)雜零件的加工提供了解決之道,一次裝夾可實現(xiàn)多面加工以及一坐標(biāo)聯(lián)動加工,提高了加工精度和加工效率。加工中心主軸銑削加工時最高轉(zhuǎn)速為12000rpm,磨削加工時為10000rpm。
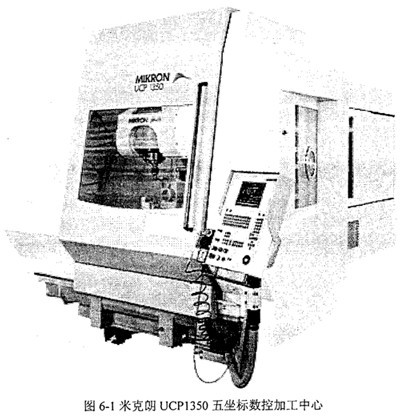
UCP1350采用了新的海登海因HeidenhainTNC426M數(shù)控系統(tǒng)。此系統(tǒng)支持海登海因純文本和DIN或ISO語言進行車間現(xiàn)場編程,并支持并行模式,當(dāng)機床在加工工件時,可進行其他程序的編制,通過“固有程序操作”功能,控制系統(tǒng)能對未經(jīng)數(shù)控方式定義的工件進行編程工作。內(nèi)外空間正弦滾疲道的數(shù)控加工程序參見附錄。
由于圓柱正弦活齒減速器徑向尺寸小,在現(xiàn)有國產(chǎn)銑刀的條件下,加工殼體的內(nèi)空間正弦滾道具有很大的難度,本文提出一種加工方案,較好的解決了這個難題。采用五坐標(biāo)數(shù)控加工中心,將球狀銑刀傾斜一定角度,斜插進殼體內(nèi)圓柱面進行銑削加工,其加工位置示意圖如圖6-2。
由于球狀銑刀的刀刃部分為半球頭形狀,為避免球頭銑刀的刀柄與殼體內(nèi)壁發(fā)生干涉,導(dǎo)致內(nèi)空間正弦滾道被銑削出平面,則空間正弦曲線的平衡位置到殼體端面的距離L應(yīng)滿足一定的條件,由圖6-2中各參數(shù)的關(guān)系,可以得到

根據(jù)空間正弦滾道的形成原理,銑刀中心沿空間正弦軌跡曲線運動的同時,刀具自身作旋轉(zhuǎn)運動,并沿徑向方向進給運動加工出滾道槽深,則銑刀的刀刃包絡(luò)出內(nèi)外空間正弦滾道的齒廓曲面,也即完成了空間正弦滾道的銑削工藝。
為保證空間正弦滾道的加工精度,工件經(jīng)過車削、銑削及高頻淬火等工藝流程后,必須對空間正弦滾道進行精磨。對內(nèi)空間正弦滾道的磨削是比較困難的工藝流程,本文根據(jù)滾道及殼體內(nèi)圓柱面的形狀尺寸,進行了非標(biāo)球頭磨具的設(shè)計。該非標(biāo)球頭磨具的材質(zhì)選用金屬基立方氮化硼(CBN),CBN濃度為100%,粒度為80目。其制造的工藝流程為:將立方氮化硼顆粒溶入液化的金屬基(銅)中,澆注在特定的模具中,冷卻凝固后,將金屬基CBN球頭與鋼質(zhì)刀柄用銀焊接在一起,最后采用電火花工藝將球頭按一定精度加工成型,由此更好的保證了球頭磨具的型位公差。為防止磨削時產(chǎn)生的積屑降低磨具的磨削硬度及精度,在磨具的球頭部位還設(shè)計有排屑槽。加工成型后的金屬基CBN球頭磨具見圖6-3。最終加工成型的主動軸、導(dǎo)架、殼體、其它關(guān)鍵件及裝配后的減速器樣機見圖6-4~圖6-8。
6.2傳動效率試驗研究
6.2.1試驗原理
機械傳動件的性能是工程界十分重視的一個問題,它直接影響產(chǎn)品成本及能源消耗,每個設(shè)計師都希望自己設(shè)計的機器是一臺高效率,噪聲低,振動小,溫升低的機械。但是,由于機器結(jié)構(gòu)等因素的影響,實際機器很難達到理想的計算效率及其它設(shè)計參數(shù),實際機器效率受加工精度和裝配精度及使用條件等因素影響將低于計算效率,這就需要進行試驗研究,以測量實際機器的效率值和與其相關(guān)的參數(shù),給傳動裝置的選擇及改進設(shè)計提供數(shù)據(jù)。為此,本文對圓柱正弦活齒減速器樣機進行了傳動比及傳動效率試驗研究,試驗裝置的工乍原理如圖6-9所示。試驗臺的實物照片如圖6-10所示。
試驗臺采用直流電動機驅(qū)動,磁粉制動器作為加載裝置,電動機通過調(diào)節(jié)穩(wěn)流電源電流控制磁粉制動器加載轉(zhuǎn)矩的大小。為了方便準(zhǔn)確的測定減速器的傳動效率,在試驗臺的輸入端與輸出端各安裝一臺磁電式轉(zhuǎn)矩轉(zhuǎn)速傳感器,傳感器將輸入輸出軸上的轉(zhuǎn)矩和轉(zhuǎn)速變成電信號,并由轉(zhuǎn)矩轉(zhuǎn)速測量儀顯示出輸入軸轉(zhuǎn)矩M1、轉(zhuǎn)速n1、功率P1及輸出軸的轉(zhuǎn)矩M2、轉(zhuǎn)速n2、功率P2的測量值。則被測減速器的傳動效率為
η=P2/P1 (6-2)
式中 P
1——輸入、輸出功率P
1=
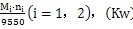
圖6-10 傳動效率試驗裝置(圖略)
6.2.2扭矩轉(zhuǎn)速測量裝置
試驗臺為了同時測量轉(zhuǎn)矩和轉(zhuǎn)速,需使用可同時測量兩種物理量的傳感器。目前常用磁電式傳感器來同時測量轉(zhuǎn)速轉(zhuǎn)矩,其根據(jù)磁電轉(zhuǎn)換和相位差原理,將轉(zhuǎn)矩,轉(zhuǎn)速機械量轉(zhuǎn)換成兩路有一定相位的電壓訊號,能直接測量各種動力機械的轉(zhuǎn)矩與轉(zhuǎn)速,具有測量精度高(誤差±0.2%),操作簡便,顯示直觀,測量范圍廣等優(yōu)點,可以測量軸靜止?fàn)顟B(tài)至額定轉(zhuǎn)速范圍的轉(zhuǎn)矩,它輸出功率大且性能穩(wěn)定,具有一定的工作帶寬,因而得到普遍應(yīng)用。
圖6-11為磁電式相位差型轉(zhuǎn)矩轉(zhuǎn)速傳感器的結(jié)構(gòu)示意圖,它由機座、端蓋、扭力軸、內(nèi)齒輪、外齒輪、磁鋼、線圈軸承等組成。內(nèi)齒輪、磁鋼固定在套筒上,線圈固定在端蓋上,外齒輪固定在扭力軸上,當(dāng)內(nèi)外齒輪發(fā)生相對轉(zhuǎn)動時,由于磁通不斷變化,在線圈中便感應(yīng)出近似正弦波的感應(yīng)電勢ul、u2,兩感應(yīng)電勢的初始相位差是恒定的,考慮到正反加載, 設(shè)計在大約180°位置上,當(dāng)加上扭力時,扭力軸發(fā)生扭轉(zhuǎn)變形,在彈性范圍內(nèi)外加扭矩與機械扭轉(zhuǎn)角成正比,這時ul、u2訊號的相位差要發(fā)生變化,即

(6-3)
當(dāng)傳感受器的扭矩增加到額定值時,變化的相位

大約為90°。因此,測量出

就等于間接測量出軸上的外加轉(zhuǎn)矩,寧產(chǎn),傳感器就實現(xiàn)了把機械量的扭角變化轉(zhuǎn)化成電子量的相位差變化的過程。
6.2.3試驗加載裝置
采用磁粉制動器作為試驗的加載裝置。磁粉制動器由轉(zhuǎn)子、機殼、激磁線圈、磁粉組成,其結(jié)構(gòu)如圖6-12所示。在激磁線圈不通電流時,不產(chǎn)生磁通,磁粉呈自由狀態(tài)。當(dāng)軸轉(zhuǎn)動時,由于離心力的作用,使磁粉散布在轉(zhuǎn)動件與機殼之間,若此時激磁線圈通電流,則在線圈周圍產(chǎn)生磁場,轉(zhuǎn)動件與機殼間的磁粉沿磁通方向連接成鏈狀,由于磁粉間的結(jié)合力,使工作面之間產(chǎn)生摩擦力,從而形成制動力矩,起到加載的作用。該力矩與激磁電流的大小基本成正比,故通過調(diào)節(jié)激磁線圈的電流大小可在一定范圍內(nèi)改變制動力矩的大小。
6.2.4試驗結(jié)果分析
進行減速器效率試驗前,首先讓減速器在輸入轉(zhuǎn)速為500rpm的條件下,空載跑合4個小時,觀察運轉(zhuǎn)正常后,進入試驗的準(zhǔn)備階段。為測得準(zhǔn)確試驗數(shù)據(jù)必項對轉(zhuǎn)矩轉(zhuǎn)速測量儀進行常數(shù)輸入和轉(zhuǎn)矩調(diào)零設(shè)置,一切準(zhǔn)備完畢后,開始對減速器進行試驗測試。當(dāng)輸入軸轉(zhuǎn)速取不同值時計算出減速器樣機的傳動比及樣機總評傳動比如表6-1所示,通過分析測試數(shù)據(jù)可知,經(jīng)實測最大的傳動比誤差為-0.0148,平均傳動比誤差為-0.0078。表明樣機的傳動比準(zhǔn)確,傳動精度高。經(jīng)分析可知,正弦滾道的加工精度是造成整機傳動誤差的主要原因。
表6-1 傳動比測試結(jié)果
輸入轉(zhuǎn)速(rpm) |
400 |
500 |
600 |
700 |
800 |
900 |
1000 |
1200 |
1500 |
傳動比平均值 |
輸出轉(zhuǎn)速(rpm) |
81.2 |
100.5 |
120.2 |
140.7 |
161.1 |
182.3 |
202 |
241.8 |
305 |
4.961 |
傳動比 |
4.926 |
4.975 |
4.99 |
4.965 |
4.969 |
4.945 |
4.95 |
4.963 |
4.967 |
當(dāng)輸入轉(zhuǎn)速為500rpm時,通過磁粉制動器對減速器施加不同的載荷值,得到一系列輸入輸出轉(zhuǎn)矩、輸入輸出功率及效率如表6-2所示。
表6-2 傳動效率測試結(jié)果
輸入轉(zhuǎn)矩(N·m) |
0.325 |
0.426 |
0.52 |
0.628 |
0.712 |
0.81 |
0.923 |
效率平均值 |
輸入功率(w) |
17 |
22.3 |
27.2 |
32.9 |
37.3 |
42.4 |
48.3 |
輸入轉(zhuǎn)矩(N·m) |
1.493 |
1.975 |
2.423 |
2.933 |
3.336 |
3.811 |
4.352 |
輸入功率(w) |
15.6 |
20.7 |
25.4 |
30.7 |
34.9 |
39.9 |
45.6 |
效率η |
0.919 |
0.927 |
0.932 |
0.934 |
0.937 |
0.941 |
0.943 |
0.933 |
同樣方式測得當(dāng)輸入轉(zhuǎn)速分別為700rpm、900 rpm、1100 rpm、1300 rpm、1500 rpm時,減速呂樣機的平均效率隨輸入轉(zhuǎn)速變化曲線如圖6-13。通過測試結(jié)果表明,在低中速情況下,減速器的傳動效率受其轉(zhuǎn)速的影響不明顯,由于此時潤滑脂溫度較低,隨著轉(zhuǎn)速的增加,減速器的傳動效率略有提高,其平均值在93%以上,由引說明本文設(shè)計的減速器具有較高的傳動效率。
6.3本章小結(jié)
1.在理論分析的基礎(chǔ)上,經(jīng)過多目標(biāo)優(yōu)化設(shè)計,最終確定減速器的結(jié)構(gòu)參數(shù),并繪制出減速器的裝配圖和零件圖。與哈爾濱建成集團合作加工制造出一臺樣機;
2.提出在小半徑內(nèi)圓柱面上加工空間正弦滾道的方法,為提高加工精度,設(shè)計并制造出非標(biāo)CBN球頭磨具;
3.設(shè)計了試驗方案,設(shè)計、加工了與該減速器配套的試驗輔助裝置,驗裝了試驗臺。通過試驗結(jié)果表明,該減速器具有較高的傳動精度和傳動效率。