第3章 滾柱活齒減速器的設計及計算機輔助分析
3.1引言
本章在活齒傳動理論分析的基礎上,針對井下驅(qū)動螺桿泵采油系統(tǒng)的實際技術要求,設計最大外徑114mm、傳動比為9、工作井深1000m的滾柱活齒減速器以滿足油田生產(chǎn)需要。
首先,給出根據(jù)滾柱活齒傳動的運動條件和強度條件設計減速器的方法,并根據(jù)這些約束條件初步確定減速器的參數(shù)。為準確驗證所設計的減速器能否實現(xiàn)預定的設計要求,本章擬采用有限元分析的方法,針對減速器關鍵零件進行靜力學分析和模態(tài)分析,以驗算其強度是否滿足要求,確定輸入、輸出軸正常工作時能否受激共振。
同時,為避免樣機加工后發(fā)現(xiàn)問題而造成損失,縮短設計周期,在樣機設計完成后,擬采用虛擬樣機仿真技術對其進行運動學仿真,以驗證其能否實現(xiàn)確定的相對運動。仿真成功后,繪制出全部零件圖和裝配圖并加工樣機。
3.2 減速器結構的設計
為簡化樣機結構,將波發(fā)生器與輸入軸設計成一個零件,統(tǒng)稱輸入軸。將中心輪固定,選擇輸入軸和輸出軸旋轉(zhuǎn)方向相同。由于波發(fā)生器部分屬偏心結構,工作時要承受很大的徑向力,為改善支承的受力情況,采用雙排相差為180°的滾柱活齒結構,不但使慣性力和慣性力矩完全平衡,而且保證整機的嚙合力和嚙合力矩平衡。
由于中心輪內(nèi)齒面要同時與相差為180°的兩排活齒嚙合而且中心輪的齒形加工采用線切割工藝,所以中心輪沿軸線上各截面形狀應保持一致。確定采用的結構后,根據(jù)運動條件和強度條件初步確定減速器的具體參數(shù)。
3.2.1 運動條件
3.2.1.1 中心輪理論齒廓曲線不頂切條件 由于中心輪理論齒廓曲線是滾柱活齒中心運動軌跡的等距線,所以當滾柱活齒中心運動軌跡的最小曲率半徑ρmin≥r2時,活齒可以順利地通過中心輪的齒頂;當ρmin≤r2時,中心輪的理論齒廓曲線要發(fā)生頂切現(xiàn)象,從而使傳動終止,據(jù)此可寫出中心輪理論齒廓曲線不頂切條件:
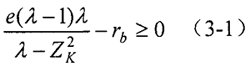
式中e——波發(fā)生器偏心圓的偏心距;
λ——激波系數(shù),λ=(r1+r2)/e;
r1——波發(fā)生器半徑;
ZK——中心輪齒數(shù);
r2——滾柱活齒半徑。
連續(xù)的齒廓曲線有傳動平穩(wěn)、參與嚙合的齒數(shù)多等優(yōu)點,所以設計活齒傳動時,一般總是希望得到連續(xù)的齒廓曲線,即使之滿足式(3-1)。
3.2.1.2 偏心距e和徑向間隙c是活齒減速器的重要參數(shù),減速器的結構形式和傳動比不同,偏心距e和徑向間隙c 的值也不同,其取值應按表3-1中的參數(shù)優(yōu)先選取。
表3-1 徑向間隙c、偏心距e的優(yōu)選值(mm)
偏心距 |
0.65 |
0.75 |
0.85 |
1 |
1.25 |
1.5 |
1.75 |
2 |
2.5 |
3 |
3.5 |
4 |
徑向間隙 |
0.9 |
1.0 |
1.1 |
1.2 |
1.3 |
1.4 |
1.5 |
1.6 |
1.7 |
1.8 |
1.9 |
2 |
偏心距 |
4.5 |
5 |
5.5 |
6 |
6.5 |
7 |
7.5 |
8 |
9 |
10 |
11 |
12 |
徑向間隙 |
2.1 |
2.2 |
2.3 |
2.4 |
2.5 |
2.6 |
2.7 |
2.8 |
2.9 |
3 |
3.1 |
3.2 |
3.2.1.3 滾柱活齒連續(xù)傳動條件 為保證活齒在工作開始位置(中心輪齒頂)傳動連續(xù),活齒在與中心輪齒頂接觸的同時,與活齒架應保持接觸。由幾何條件可知,活齒架內(nèi)圓半徑最大值即活齒工作起始位置連續(xù)傳動條件為:
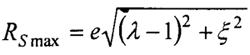
式中 ξ——活齒系數(shù),ξ=rb/e;
RSmax——活齒架內(nèi)圓半徑最大值。
活齒架內(nèi)表面和波發(fā)生器外輪廓面之間不應該發(fā)生運動干涉,不發(fā)生運動干涉的條件為:
RSmin=e(1+λ-ξ)
式中RSmin——活齒架內(nèi)圓半徑最小值。
上兩式聯(lián)立,可求出活齒架內(nèi)圓半徑RS的尺寸范圍,見式(3-2)。

同樣方法可得活齒工作結束位置(中心輪齒根)連續(xù)傳動條件:

式中RMmin——活齒架外圓半徑最小值。
活齒架外表面和中心輪的齒頂不發(fā)生運動干涉的條件:

式中RMmax——活齒架外圓半徑最大值。
上兩式聯(lián)立,可求出活齒架外圓半徑RM的尺寸范圍,見式(3-3)。

3.2.1.4 活齒架的最小壁厚 聯(lián)立活齒工作起始位置和結束位置時的連續(xù)傳動條件,可得活齒架薄壁筒的最小壁厚為:

3.2.2 強度條件
3.2.2.1 活齒與波發(fā)生器間表面接觸疲勞強度
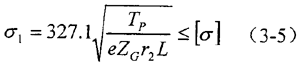
式中TP——波發(fā)生器的輸入力矩,N·m;
ZG——活齒數(shù);
L——活齒工作寬度,m;
[σ]——考慮壽命、載荷等因素的許用應力,[σ]=1423MPa。
3.2.2.2 中心輪接觸疲勞強度

式中ρ——綜合曲率半徑,
ρ2——取中心輪齒廓曲率半徑最小值,m;
E——彈性模量,2.06×1011N/m2;
FKmax——活齒對中心輪的作用力,N。
在齒根附近(拐點以下)嚙合時,綜合曲率半徑ρ中取減號,在齒頂附近(拐點以上)嚙合時,綜合曲率半徑ρ中取加號。
3.2.2.3 活齒架接觸疲勞強度和剪切強度 剪切強度為:
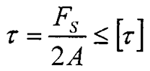
式中A——每個活齒槽的橫截面積,A≈2r2(RM-RS);
FS——活齒對活齒架作用力,N;
[τ]——許用剪應力,MN/m2。
接觸疲勞強度:
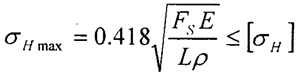
式中E——彈性模量,2.06×1011N/m2。
首先根據(jù)上述運動條件初步確定幾何參數(shù),然后采用強度條件校核。經(jīng)分析可知,參數(shù)可行域很小,考慮到波發(fā)生器偏心距e、徑向間隙c等參數(shù)需圓整為表3-1中的優(yōu)選值,初步確定主要參數(shù)如下:波發(fā)生器偏心距e=1.5mm,波發(fā)生器半徑r1= 30mm,r2=8mm,活齒數(shù)ZG=9,中心輪齒數(shù)ZK=8,活齒工作寬度L=60mm。
3.3 滾柱活齒減速器有限元強度分析和模態(tài)分析
有限元法(FEM)是一種采用計算機求解結構靜、動態(tài)力學特性等問題的數(shù)值解法,現(xiàn)己廣泛應用于結構、熱、電磁場、流體等分析領域,成為現(xiàn)代機械產(chǎn)品設計中的一種重要工具。當前,國際上最權威的大型商用有限元分析軟件是美國ANSYS公司的ANSYS軟件。
進行有限元分析,首先要建立被研究對象的實體模型。ANSYS提供了三種方法創(chuàng)建實體模型:自下而上法(Bottom-up)、自上而下法(Top-down)和從其他CAD系統(tǒng)導入法。
自下而上法是先創(chuàng)建關鍵點,然后依次創(chuàng)建相關的線、面和體等圖元。自頂而下法是可以直接創(chuàng)建最高級的圖元,即幾何體素。當用戶定義了一個體素時,程序會自動定義相關的面、線和關鍵點。用戶可以利用這些高級圖元直接構造幾何模型。在ANSYS建模過程中,自頂而下的建模方法和自底而上的建模方法是可以自由組合使用的,從而使模型的創(chuàng)建更加方便。
另外,ANSYS提供了與其他CAD系統(tǒng)的強大接口,用戶也可以在擅長的CAD系統(tǒng)里建立實體模型,然后把該模型以某一種格式導入到ANSYS中,一旦模型成功導入后,就可以象在ANSYS 中創(chuàng)建的模型那樣對此模型進行網(wǎng)格劃分。這些接口程序是由ANSYS公司或CAD供應商編寫的軟件。由ANSYS公司可以得到下列軟件的譯碼器;AutoCAD、CADAM、CADKEY和Pro/ENGINEER 。
其中值得注意的是ANSYS-Pro/ENGINEER接口,因為它提供了以執(zhí)行部件為基礎的參數(shù)化優(yōu)化設計的功能。該功能允許由部件為基礎的參數(shù)化Pro/ENGINEER模型開始,用ANSYS程序?qū)ζ溥M行優(yōu)化,并以一個優(yōu)化的Pro/ENGINEER 模型結束,且仍是以部件為基礎的參數(shù)化模型。
3.3.1 減速器三維實體模型的建立
無論進行有限元分析還是虛擬樣機仿真,都要求首先建立減速器的三維實體模型。雖然ANSYS 在有限元分析方面技術領先,但其在三維實體建模方面并不比專業(yè)的CAD系統(tǒng)方便,甚至對于復雜的實體模型還要借助第三方軟件才能完成。由于滾柱活齒減速器的中心輪和活齒架等零件的實體特征較復雜,故考慮采用第三方軟件來完成。
工程用三維實體建模軟件主要有Pro/ENGINEER、Ideas、UG等。其中美國PTC公司開發(fā)的Pro /ENGINEER 是世界上第一個基于特征的參數(shù)化實體建模軟件,其在三維建模、尤其是復雜曲面的造型方面處于領先水平。所以減速器擬采用Pro/ENGINEER進行建模。
無論進行有限元分析還是虛擬樣機仿真,我們只需研究與減速器工作直接相關的波發(fā)生器、活齒、活齒架和中心輪等關鍵零件,而忽略端蓋、端套、軸承等輔助零件,據(jù)此建立減速器三維實體模型及其分解圖見圖3-1和圖3-2。
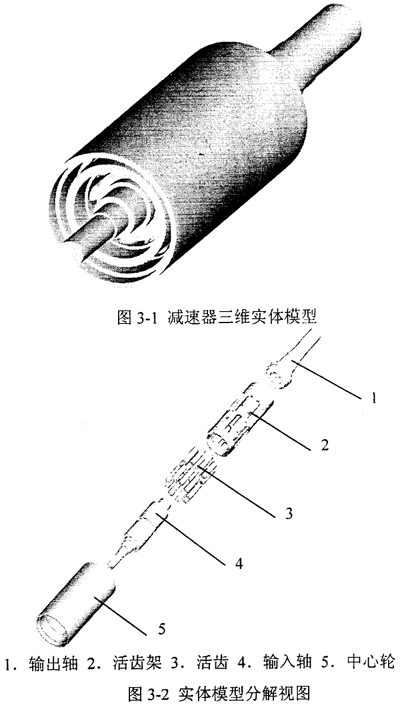
3.3.2 減速器關鍵件的有限元強度分析
3.3.2.1 活齒架的強度分析 采用平臺為Pentium IV 1.7GHz CPU 、128MDDR SDRAM內(nèi)存、NVIDIA Geforce2 MX/MX4OO顯卡、Windows XP操作系統(tǒng)和ANSYS5.7 軟件進行分析求解。
將Pro/ENGINEER中創(chuàng)建的活齒架模型以IGES格式導入ANSYS中,并作適當拓撲修補,以完成預處理中實體模型的建立。
根據(jù)問題的性質(zhì)和模型的復雜程度,選用Solid95單元(見圖3-3)。該單元是三維的20個節(jié)點的結構單元,可以在保證計算精度的前提下允許實體中不規(guī)則的形狀存在。每個節(jié)點存在三個自由度:X、Y和Z方向的移動,可應用于塑性、脆性、大變形和大應變等問題。
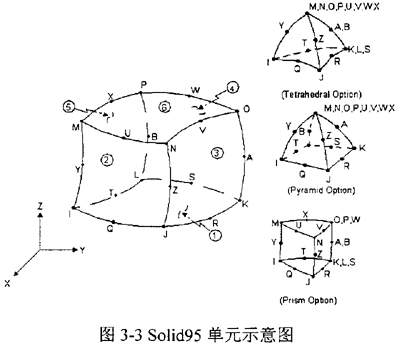
設定材料屬性為線性各向同性、楊氏模量為2.06×1011N/m2、泊松比為0.3,采用自由網(wǎng)格劃分并設定劃分網(wǎng)格精度為7。在每個工作活齒所在活齒槽中分別加載4400N,限制輸出端節(jié)點的全部自由度,劃分網(wǎng)格并加載后的有限元模型見圖3-4。求解后,在后處理中各節(jié)點的總位移等值圖見圖3-5,最大位移在節(jié)點688處,值為0.71μm。各節(jié)點的綜合應力等值圖見圖3-6,其中最大綜合應力在節(jié)點69處,大小為599846N/m2,小于許用應力。
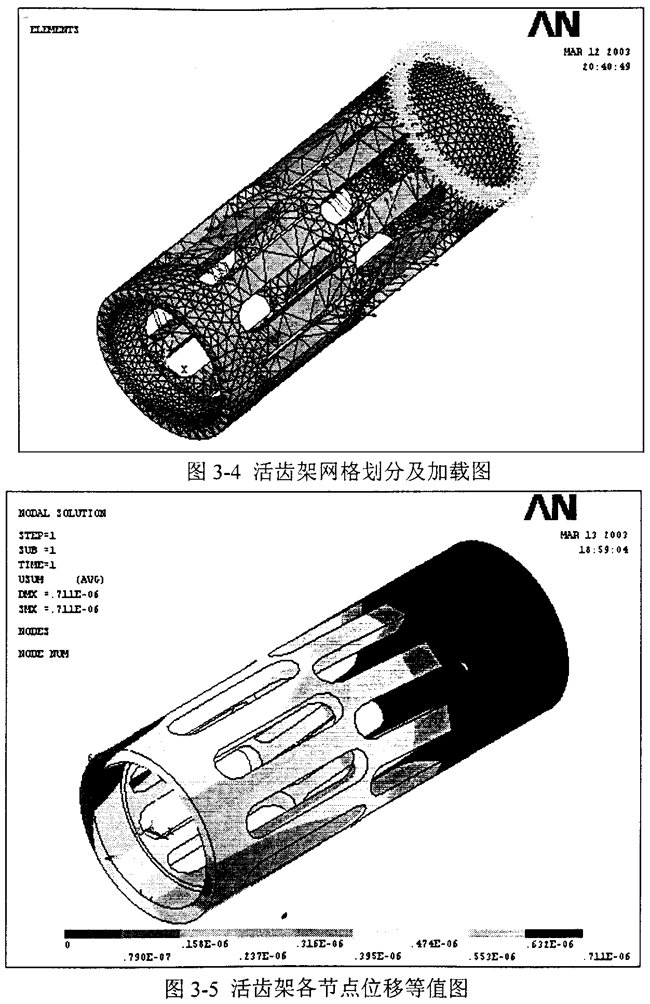
3.3.2.2輸入輸出軸的強度分析 同樣將Pro/ENGINEER中創(chuàng)建的輸入軸和輸出軸模型以IGES格式導入ANSYS中,并作適當拓撲修補,完成預處理中實體模型的建立。
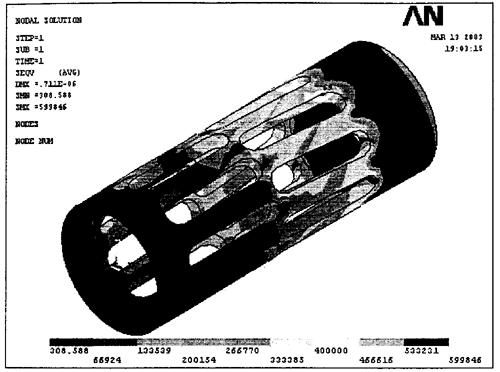
全面考慮計算精度與計算機資源,選用Soild45單元(圖3-7 ),該單元有8個節(jié)點,每個節(jié)點有X、Y和Z三個方向的自由度。同樣設定材料屬性,采用自由網(wǎng)格劃分并設定劃分網(wǎng)格精度為9。對輸入軸限制輸入端節(jié)點的全部自由度,在另一端施加工作扭矩,劃分網(wǎng)格并加載后的有限元模型見圖3-8。求解后,得各節(jié)點的總位移等值圖見圖3-9,最大位移在節(jié)點420處,值為0.254mm。
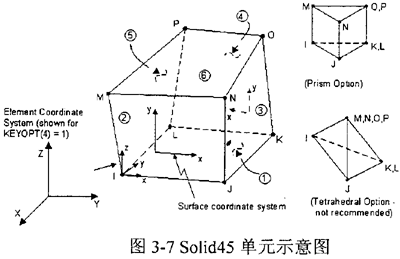
各節(jié)點的綜合能力等值圖見圖3-10,其中平均綜合應力為75043N/mm2,遠小于材料的許用應力。
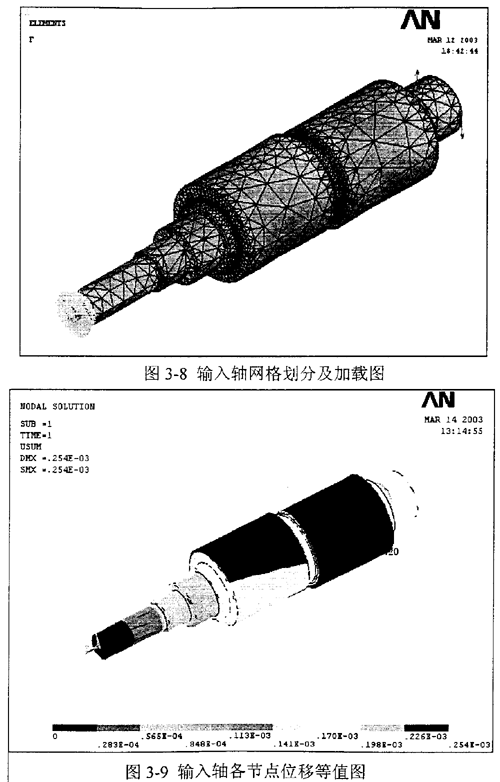
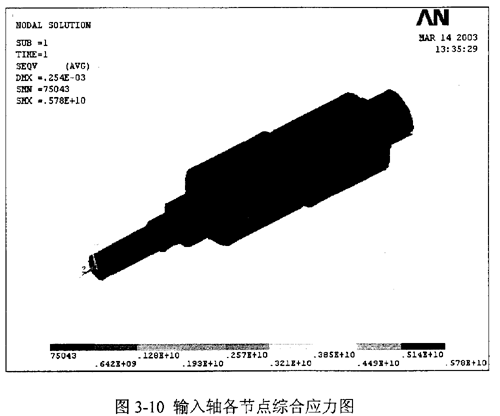
同樣,輸出軸劃分網(wǎng)格并加載后見圖3-11,各節(jié)點位移圖和綜合應力圖分別見圖3-12和圖3-13。查詢可知輸出軸了大位移在節(jié)點49處,位移值為0.333mm。平均綜合應力為1.5MN/mm2,遠小于許用應力。
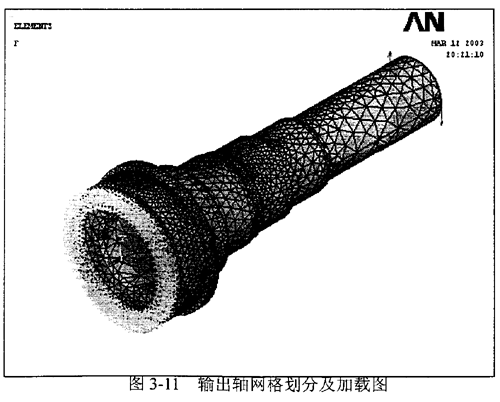
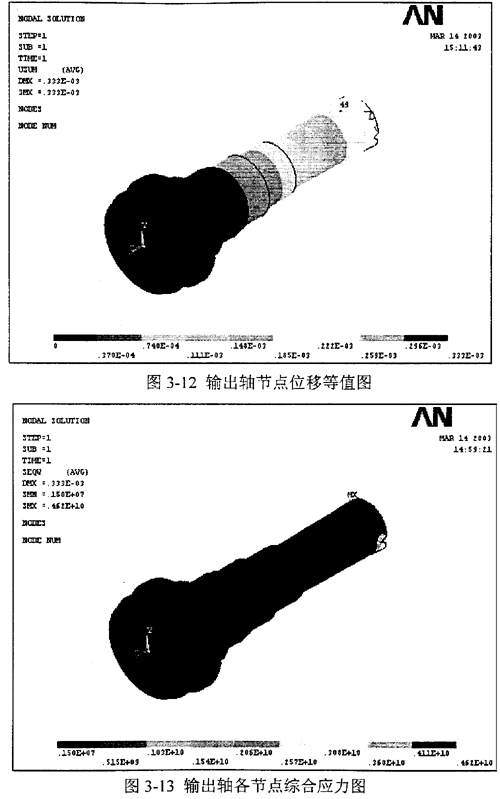
上一頁
下一頁
|