第4章 油膜浮動(dòng)均載的兩級(jí)三環(huán)減速器的設(shè)計(jì)
4.1引言
三環(huán)減速器運(yùn)動(dòng)和受力均勻且充分地利用了功率分流和內(nèi)嚙合多齒接觸的原理,因此,三環(huán)減速器的承載能力大。采用三片內(nèi)齒環(huán)板偏心之間呈180°相位角的布置形式,能夠?qū)崿F(xiàn)慣性力和慣性力矩的完全平衡,也保證了整機(jī)的嚙合力和嚙合力產(chǎn)生的力矩平衡,采用雙軸輸入可使三環(huán)減速器的各環(huán)板載荷分布均勻,兩高速軸的轉(zhuǎn)臂軸承受力減少,效率提高。但由于不可避免的制造和安裝誤差及動(dòng)力傳遞過程中出現(xiàn)的零部件變形,使得三片內(nèi)齒環(huán)板之間的作用單位寬度上的載荷分配不均勻,引起動(dòng)載荷增加,導(dǎo)致振動(dòng)加劇,造成齒面點(diǎn)蝕、軸承損壞、齒輪箱發(fā)熱,甚至發(fā)生事故。針對(duì)上述問題,本文提出了一種同步帶傳動(dòng)作為一級(jí)傳動(dòng)的完全平衡均載減振的兩級(jí)三環(huán)減速器,該減速器齒輪傳動(dòng)部分的慣性力和慣性力矩完全平衡,同步帶傳動(dòng)實(shí)現(xiàn)了三環(huán)傳動(dòng)的雙軸輸入和功率分流及均載,并克服了死點(diǎn)問題,油膜浮動(dòng)實(shí)現(xiàn)了三環(huán)減速器均載和減振。本章對(duì)該減速器研制中的有關(guān)問題,特別是兩級(jí)傳動(dòng)的設(shè)計(jì)和油膜浮動(dòng)均載裝置的設(shè)計(jì)進(jìn)行了系統(tǒng)的研究。
4.2 兩級(jí)三環(huán)減速器的結(jié)構(gòu)分析
4.2.1結(jié)構(gòu)分析
兩級(jí)三環(huán)減速器的基本結(jié)構(gòu)如圖1-6所示,它分為兩級(jí)傳動(dòng),一級(jí)傳動(dòng)由小同步帶輪12、同步齒形帶9和13、大同步帶輪8和14構(gòu)成。通過嚙合,小帶輪通過平頂圓弧齒型帶帶動(dòng)兩個(gè)大帶輪旋轉(zhuǎn),實(shí)現(xiàn)一級(jí)減速和功率分流,兩個(gè)大帶輪分別帶動(dòng)三環(huán)減速器的兩曲柄軸旋轉(zhuǎn),實(shí)現(xiàn)了三環(huán)減速器的雙曲柄的同步輸入;二級(jí)傳動(dòng)由偏心輸入軸2和15、傳動(dòng)環(huán)板3、4和6、外齒輪10和輸出軸1構(gòu)成。傳動(dòng)環(huán)板上的內(nèi)齒圈與輸出軸上的外齒輪相嚙合,形成大傳動(dòng)比,實(shí)現(xiàn)二級(jí)減速及動(dòng)力傳遞。三個(gè)內(nèi)齒環(huán)板中的兩側(cè)環(huán)板3和6與中間環(huán)板4相差180°,且兩側(cè)各環(huán)板厚度為中間環(huán)板的1/2,這樣可保證運(yùn)轉(zhuǎn)時(shí)它們的慣性力和慣性力矩理論上完全平衡。三環(huán)減速器輪齒嚙合的均載是采用在兩曲柄軸偏心套外表面和轉(zhuǎn)臂軸承內(nèi)表面之間插入一個(gè)浮動(dòng)圓筒16,在曲柄軸旋轉(zhuǎn)時(shí),偏心套和圓筒之間、圓筒和轉(zhuǎn)臂軸承內(nèi)表面之間均形成了動(dòng)壓油膜,油膜的彈性變形使得內(nèi)齒環(huán)板浮動(dòng),補(bǔ)償減速器的制造和安裝誤差以及傳動(dòng)時(shí)產(chǎn)生的零部件變形。
4.2.2傳動(dòng)比計(jì)算
筆者設(shè)計(jì)的新型三環(huán)減速器為兩級(jí)傳動(dòng),根據(jù)機(jī)械傳動(dòng)的理論,一級(jí)帶傳動(dòng)的速比取1~3較好,二級(jí)三環(huán)傳動(dòng)的速比為11~99,這使得總速比的范圍寬,從11~297,當(dāng)作為一系列減速比的產(chǎn)品時(shí),該減速器可采用改變Z01和Z02齒數(shù)的方法來達(dá)到不同的減速比,同時(shí),該減速器通過一級(jí)減速后,三環(huán)傳動(dòng)的輸入轉(zhuǎn)速將降低,這能減少整機(jī)的振動(dòng)和噪音?偟膫鲃(dòng)比i包括兩部分,第一部分是同步帝傳動(dòng)的傳動(dòng)比i1,
;第二部分是三環(huán)傳動(dòng)的傳動(dòng)比i2,
。
兩級(jí)三環(huán)減速器的總傳動(dòng)比i為:

式中 Z1,Z2——分別為外齒輪和內(nèi)齒環(huán)板的齒數(shù);
Z01,Z02——分別為小帶輪和大帶輪的齒數(shù)。
4.3 同步帶傳動(dòng)的設(shè)計(jì)
1. 同步帶的設(shè)計(jì) 平頂圓弧同步帶的齒面受力和應(yīng)力分布均勻,傳動(dòng)的多邊形效應(yīng)較弱,振動(dòng)和噪聲低,承載能力大。本文選用平頂圓弧齒同步帶。為了同理有的三環(huán)式減速器進(jìn)行性能比較,本文以SH145型三環(huán)式減速器作為對(duì)象,即:以現(xiàn)有的SH145三環(huán)式減速器的性能參數(shù)作為設(shè)計(jì)依據(jù)。其參數(shù)為:傳動(dòng)比i=40.5;輸入轉(zhuǎn)速n1=1500r/min;輸出轉(zhuǎn)矩T2=0.875kN·m;客定功率PN=3.58kW。新機(jī)型:傳動(dòng)比i=42;輸入轉(zhuǎn)速n1=1500r/min;輸出轉(zhuǎn)矩T2=0.875kN·m;額定功率PN=3.42kW。
由設(shè)計(jì)手冊(cè)可確定出:
電機(jī)型號(hào)為:Y112M-4;同步轉(zhuǎn)速為:n1=1500r/min;滿載轉(zhuǎn)速為:n=1440r/min。
圓弧齒同步帶的型號(hào)為:5M。節(jié)距pb=5,節(jié)線長(zhǎng)度LP=615mm,同步帶齒數(shù)Zb=123,實(shí)際中心距a=154.132,帶寬bs=30mm的帶兩條。
2.同步帶輪的設(shè)計(jì) 與同步帶相對(duì)應(yīng)的帶輪的型號(hào):5M。節(jié)距pb=5,小帶輪的齒數(shù)Z01=40,大帶輪的齒數(shù)Z02=80,帶輪的其它參數(shù)見表4-1和圖4-1。
表4-1 一級(jí)傳動(dòng)參數(shù)
型號(hào) |
節(jié)距Pb(mm) |
齒槽深hg
(mm) |
齒槽圓弧
半徑Rb
(mm) |
齒頂圓角
半徑ri
(mm) |
外圓齒槽寬
b0
(mm) |
節(jié)頂距δ
(mm) |
齒形角
2β
(°) |
5M |
5 |
2.06 |
1.6 |
0.35 |
3.2 |
0.57 |
14 |

4.4三環(huán)齒輪傳動(dòng)的設(shè)計(jì)
4.4.1主要參數(shù)的確定
少齒差行星齒輪傳動(dòng)是內(nèi)嚙合漸開線圓柱齒輪副在內(nèi)齒輪和外齒輪齒數(shù)差很少時(shí)所組成的行星齒輪機(jī)構(gòu)。三環(huán)傳動(dòng)是少齒差傳動(dòng)的一種,早期開發(fā)的三環(huán)減速器的內(nèi)齒圈由三片組成,相互錯(cuò)位120°偏心安裝,動(dòng)力由兩根輸入軸同時(shí)帶動(dòng)三片內(nèi)齒圈輸入,再通過一個(gè)大齒輪輸出。本文提出的三環(huán)傳動(dòng)則不同于上面的方案,其最大區(qū)別在于完全相同的厚度為中間環(huán)板厚度1/2的兩側(cè)環(huán)板對(duì)稱布置在中間環(huán)板的兩側(cè),兩側(cè)環(huán)板與中間環(huán)板成180°相位差布置。為便于與SH145減速器對(duì)比,又考慮到兩齒差較一齒差的嚙合效率要高的特點(diǎn),本設(shè)計(jì)采用適于動(dòng)力傳動(dòng)的兩齒差方案:Zd=2;考慮到兩臺(tái)對(duì)比減速器的總傳動(dòng)比相近,故選外齒輪的齒數(shù)Z1=42;內(nèi)齒圈的齒數(shù)Z2=44;齒形角用標(biāo)準(zhǔn)齒形角a=20°;齒根高系數(shù)對(duì)重合度的影響很大,h*a減小時(shí),重合度明顯減小,設(shè)計(jì)中漸開線少齒差內(nèi)嚙合的齒頂高系數(shù)取h*a=0.8;考慮到承載和齒根應(yīng)力測(cè)試的需要,設(shè)計(jì)中取模數(shù)m=3.5mm。而嚙合角減少對(duì)提高效率有利;較大時(shí)重合度較小,對(duì)避免齒廓重迭干涉有利,因此選取時(shí)應(yīng)予綜合考慮。
由于環(huán)板上的內(nèi)齒輪是采用插齒加工的,插齒時(shí)的齒根圓的實(shí)際尺寸,是隨著所用的插齒刀的齒數(shù)及變位系數(shù)而變化的。選定上面三環(huán)式減速器內(nèi)齒輪副的基本參數(shù)Z1、Z2和a后,變位系數(shù)x1和x2是嚙合角a′的函數(shù),即根據(jù)嚙合角可確定變位系數(shù)。把變位系數(shù)xl,x2取作獨(dú)立變量,把嚙合角a′取作中間變量,并取設(shè)計(jì)要求最小的少齒差內(nèi)嚙合的重合度εα′≈1.05以及齒廓不重迭干涉系數(shù)GS′≈0.05作為內(nèi)嚙合幾何限制條件。依據(jù)文獻(xiàn)中的系數(shù)公式,采用牛頓法進(jìn)行求解,其迭代步驟為:


計(jì)算結(jié)果如下:
xl=114204, x2=1.40742, a′=37.36960°, εα=1.0500006, Gs=0.050001667, e0=4.138381916。
有關(guān)參數(shù)及公式見文獻(xiàn)。
這些參數(shù)能夠保證嚙合輪齒既避免了根切又避免了齒廓重迭干涉。薄環(huán)板的厚度取為19mm,厚環(huán)板的厚度取為38mm;環(huán)板各光孔的直徑為φ=85mm;環(huán)板和外齒輪的材料為45號(hào)鋼,調(diào)質(zhì)處理硬度為241~269HB。
由此,得到如表4-2的兩級(jí)三環(huán)減速器的基本參數(shù)。
表4-2 兩級(jí)三環(huán)減速機(jī)的基本參數(shù)表
名稱 |
特性 |
中心距L |
145mm |
小同步帶輪節(jié)圓直徑、節(jié)距、齒數(shù) |
φ63.662mm、5mm、40 |
大同步帶輪節(jié)圓直徑、節(jié)距、齒數(shù) |
φ127.324mm、5mm、80 |
同步帶(帶輪)型號(hào) |
5M |
同步帶的節(jié)線長(zhǎng)度、齒數(shù)、帶寬 |
615mm、123、30mm |
三環(huán)傳動(dòng)兩側(cè)內(nèi)齒環(huán)板模數(shù)、齒數(shù)、齒寬、變位系數(shù) |
3.5mm、44、19mm、1.4074 |
三環(huán)傳動(dòng)中間內(nèi)齒環(huán)板模數(shù)、齒數(shù)、齒寬、變位系數(shù) |
3.5mm、44、38mm、1.4074 |
三環(huán)傳動(dòng)輸出齒輪模數(shù)、齒數(shù)、齒寬、變位系數(shù) |
3.5mm、42、86mm、1.1420 |
齒頂高系數(shù) |
0.8mm |
齒形角 |
20° |
三環(huán)傳動(dòng)嚙合角 |
37.356° |
三環(huán)傳動(dòng)重合度 |
1.05 |
均載方式 |
油膜浮動(dòng) |
兩側(cè)環(huán)板浮動(dòng)環(huán)內(nèi)徑、外徑、厚度 |
φn40mm、φw45mm、19mm |
中間環(huán)板浮動(dòng)環(huán)內(nèi)徑、外徑、厚度 |
φn40mm、φw45mm、38mm |
4.4.2三環(huán)傳動(dòng)的強(qiáng)度驗(yàn)算
影響齒輪承載能力的因素是多方面的,除載荷、速度和工作狀況外,結(jié)構(gòu)形式、尺寸參數(shù)、制造和安裝精度、變形、齒廓及齒向修正、齒冕粗糙度、潤(rùn)滑、材料性質(zhì)和熱處理質(zhì)量等都有著重要影響。下面根據(jù)漸開線圓柱齒輪承載能力計(jì)算方法和漸開線圓柱齒輪膠合承載能力計(jì)算方法,對(duì)筆者提出的三環(huán)傳動(dòng)進(jìn)行強(qiáng)度驗(yàn)算。
重慶大學(xué)機(jī)械傳動(dòng)國(guó)家重點(diǎn)實(shí)驗(yàn)室對(duì)三環(huán)減速器的內(nèi)齒環(huán)板所做的應(yīng)力分析以及對(duì)少齒差內(nèi)嚙合齒輪輪齒接觸問題研究均表明,三環(huán)減速器是多齒嚙合的。根據(jù)有關(guān)理論,筆者所在的課題組對(duì)完全平衡三環(huán)減速器的輪齒應(yīng)力和多齒嚙合問題進(jìn)行了理論計(jì)算和實(shí)驗(yàn)研究,結(jié)果表明,三環(huán)傳動(dòng)由于嚙合過程中的輪齒受力變形形成了多齒接觸,各齒上的載荷分布近似0°~180°間的正弦關(guān)系。圖4-2所示是接觸輪齒對(duì)的間隙單元模型。
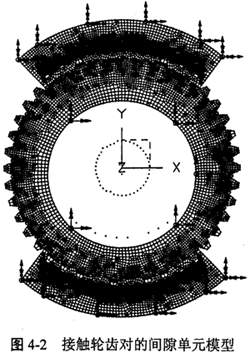
由于三環(huán)傳動(dòng)同時(shí)相嚙合的輪齒數(shù)多,對(duì)于筆者設(shè)計(jì)的樣機(jī),根據(jù)間隙圓法,筆者在確定了內(nèi)外輪齒齒廓間的最小間隙的基礎(chǔ)上,給出邊界條件并施加上載荷,應(yīng)用Ideas軟件可求得每一瞬間均有5對(duì)齒在嚙合,課題組所作的均載試驗(yàn)證實(shí),樣機(jī)瞬間嚙合的齒對(duì)數(shù)為4,因此,至少可按兩齒均勻受力來校核輪齒的齒面接觸強(qiáng)度和齒根彎曲強(qiáng)度。假設(shè)嚙合力分布均勻,這時(shí),只需校核一塊內(nèi)齒環(huán)板和輸出外齒輪的強(qiáng)度。
筆者設(shè)計(jì)的兩級(jí)三環(huán)傳動(dòng)部分的內(nèi)齒環(huán)板和輸出外齒輪的材料均為45號(hào)鋼,并進(jìn)行調(diào)質(zhì)處理,內(nèi)齒環(huán)板工作齒面HB260,取σFlim=320MPa,σHlim=700MPa;外齒輪工作齒面HB240,取σFlim=290MPa,σHlim=690MPa。根據(jù)表4-3所示的輪齒齒面接觸疲勞強(qiáng)度和齒根彎曲疲勞強(qiáng)度計(jì)算公式可進(jìn)行三環(huán)傳動(dòng)的強(qiáng)度驗(yàn)算。

查現(xiàn)代機(jī)械傳動(dòng)手冊(cè)選SHmin=1.5和SFmin=1.5。由于樣機(jī)的內(nèi)齒環(huán)板和輸出外齒輪均選用45號(hào)鋼調(diào)質(zhì)處理,根據(jù)上表提供的有關(guān)公式和樣機(jī)的實(shí)際結(jié)構(gòu)和工況,確定有關(guān)系數(shù)后,通過計(jì)算有表4-4所示的計(jì)算結(jié)果。
表4-4 三環(huán)傳動(dòng)的計(jì)算結(jié)果
項(xiàng)目 |
接觸應(yīng)力(N/mm2) |
接觸強(qiáng)度
安全系數(shù) |
彎曲應(yīng)力(N/mm2) |
彎曲強(qiáng)度
安全系數(shù) |
許用值 |
計(jì)算值 |
許用值 |
計(jì)算值 |
環(huán)板內(nèi)齒 |
397 |
74 |
5.36 |
453 |
187 |
2.42 |
輸出外齒 |
386 |
71 |
5.43 |
414 |
175 |
2.37 |
由上述三環(huán)傳動(dòng)的強(qiáng)度校驗(yàn)結(jié)果可看出,內(nèi)齒環(huán)板和輸出外齒輪的輪齒的強(qiáng)度是滿足要求的。
4.4.3三環(huán)傳動(dòng)的軸承
軸承是三環(huán)減速器的關(guān)鍵部件和主要易損件,其工作條件的好壞和使用壽命的長(zhǎng)短直接影響三環(huán)傳動(dòng)的性能。由于三環(huán)減速器的散熱面積相對(duì)較少,多軸承形式的傳動(dòng)機(jī)構(gòu)又使得它熱源較多。三環(huán)傳動(dòng)中的滾動(dòng)軸承、嚙合輪齒、傳動(dòng)環(huán)板等活動(dòng)件處的摩擦都是產(chǎn)生熱的原因。尤以滾動(dòng)軸承和輪齒嚙合處的發(fā)熱最為嚴(yán)重。在滾動(dòng)軸承的摩擦中,滾子承載時(shí)的滾子與滾道接觸區(qū)內(nèi)滑動(dòng)摩擦是發(fā)熱的主要原因,由于其工作過程中的摩擦力(矩)與滾子承載呈正比,且死點(diǎn)沖擊載荷遠(yuǎn)高于正常工作載荷,原三環(huán)減速器環(huán)板機(jī)構(gòu)過死點(diǎn)時(shí)的所受的雙向沖擊較大、制造和安裝誤差又增大了死點(diǎn)沖擊力,各環(huán)板的沖擊力和慣性力產(chǎn)生的不平衡慣性力偶作用在高速軸上,高速軸的支撐軸承承受的沖擊力也較大,使得三環(huán)減速器的振動(dòng)大、發(fā)熱嚴(yán)重。
新型三環(huán)減速器以同步帶傳動(dòng)作為一級(jí)傳動(dòng),增大了傳動(dòng)比,實(shí)現(xiàn)了新型兩級(jí)減速器的兩曲柄偏心軸同步輸入和功率分流,克服了由死點(diǎn)引起的嚴(yán)重沖擊;同時(shí),三環(huán)傳動(dòng)輸入轉(zhuǎn)速和最大嚙合力的降低,以及環(huán)板的對(duì)稱布置,使得整機(jī)的慣性力和慣性力矩完全平衡,嚙合力對(duì)振動(dòng)的影響也較小,作用在曲柄軸支撐處和轉(zhuǎn)臂軸承處的動(dòng)載荷大大減少,因而由動(dòng)載荷引起的振動(dòng)和發(fā)熱也隨之減少,使得整機(jī)的振動(dòng)和噪音以及溫升低。其結(jié)果使得新型三環(huán)減速器軸承的使用壽命延長(zhǎng),表現(xiàn)在:
1.支撐和環(huán)板轉(zhuǎn)臂軸承上的負(fù)荷減小,延長(zhǎng)了軸承的使用壽命描述圓柱滾子軸承壽命的公式為:

式中 Lh——以工作小時(shí)數(shù)計(jì)的軸承額定壽命;
n0——軸承轉(zhuǎn)速,r/min;
Cd——額定動(dòng)負(fù)荷;
P——當(dāng)量動(dòng)載荷;
P0——指數(shù),P0=10/3。
對(duì)于向心短圓柱滾子軸承的轉(zhuǎn)臂軸承,P=fPRj
式中 fP——載荷性質(zhì);
Rj——徑向載荷。
當(dāng)軸承上的負(fù)荷減小時(shí),即Rj減少,由公式(4-2)可知,軸承的壽命得以提高。
2.軸承的轉(zhuǎn)速減小,使軸承的壽命也得以提高 原三環(huán)減速器軸承的轉(zhuǎn)速也就是輸入軸的轉(zhuǎn)速n,(與環(huán)板過盈配合的的軸承外圈n2=0),新型三環(huán)減速器由于采用了一級(jí)同步帶傳動(dòng),使得偏心軸的輸入轉(zhuǎn)速為n0,n0<n,由公式(4-2)知,軸承的壽命延長(zhǎng)了。
3.油膜浮動(dòng)減小了環(huán)板軸承孔軸線歪斜造成的滾動(dòng)軸承內(nèi)外圈傾余的不利影響 三環(huán)減速器在工作過程中,由于制造安裝誤差及零件的主形,將導(dǎo)致內(nèi)齒環(huán)板中心線相對(duì)輸出軸線偏斜,這將導(dǎo)致內(nèi)齒環(huán)板上的內(nèi)齒輪沿齒寬方向分布不均勻。而轉(zhuǎn)臂軸承的柔度,可減小誤差或變形造成的軸線偏斜的不利影響。嚙合平面上形成的偏斜角為:

式中 ck——輪齒的比剛度;
cr——環(huán)板軸承的徑向剛度;
L——軸承寬度;
B——輪齒寬度;
K′——環(huán)板內(nèi)齒輪結(jié)構(gòu)系數(shù);
a′——嚙合角;
β0——環(huán)板中心線的傾斜角。
由于油膜浮動(dòng)的結(jié)果,使轉(zhuǎn)臂軸承的徑向剛度降低,而其他參數(shù)不變,則β將降低。也就是油膜浮動(dòng)能夠減小內(nèi)輪環(huán)板的偏斜,這有利于沿內(nèi)齒環(huán)板輪齒方向的載荷均勻分布。
軸承內(nèi)外套相對(duì)傾斜,對(duì)向心短圓柱滾子軸承特別不利,主要表現(xiàn)在軸線相對(duì)傾斜使圓柱滾子產(chǎn)生不規(guī)則的轉(zhuǎn)動(dòng),滾子端部應(yīng)力增加,短時(shí)間內(nèi)滾子端部產(chǎn)生過度磨損,引起軸承破壞,有關(guān)研究表明:隨著相對(duì)傾斜角的增加,軸承使用壽命急劇下降。因此,油膜浮動(dòng)使偏斜角減小,也就是顯地延長(zhǎng)了轉(zhuǎn)臂軸承的使用壽命。
由此可見,在相同的承載能力相同的傳動(dòng)比條件下,均載后的三環(huán)減速器內(nèi)齒環(huán)板的轉(zhuǎn)臂所承受的載荷峰值大大減少,同時(shí),軸承的轉(zhuǎn)速也大大下降,偏心軸和環(huán)板產(chǎn)生的性性力減小,很自作作在轉(zhuǎn)臂上的動(dòng)載荷減少,另外,高速軸支撐軸承的轉(zhuǎn)速也大大下降,使得三環(huán)傳動(dòng)的軸承工況得到了較大改善,這樣,三環(huán)傳動(dòng)軸承的使用壽命也相應(yīng)的得到了提高。
上一頁
下一頁